- News and events
- News
- Simulations is the Fast-Track to Solutions
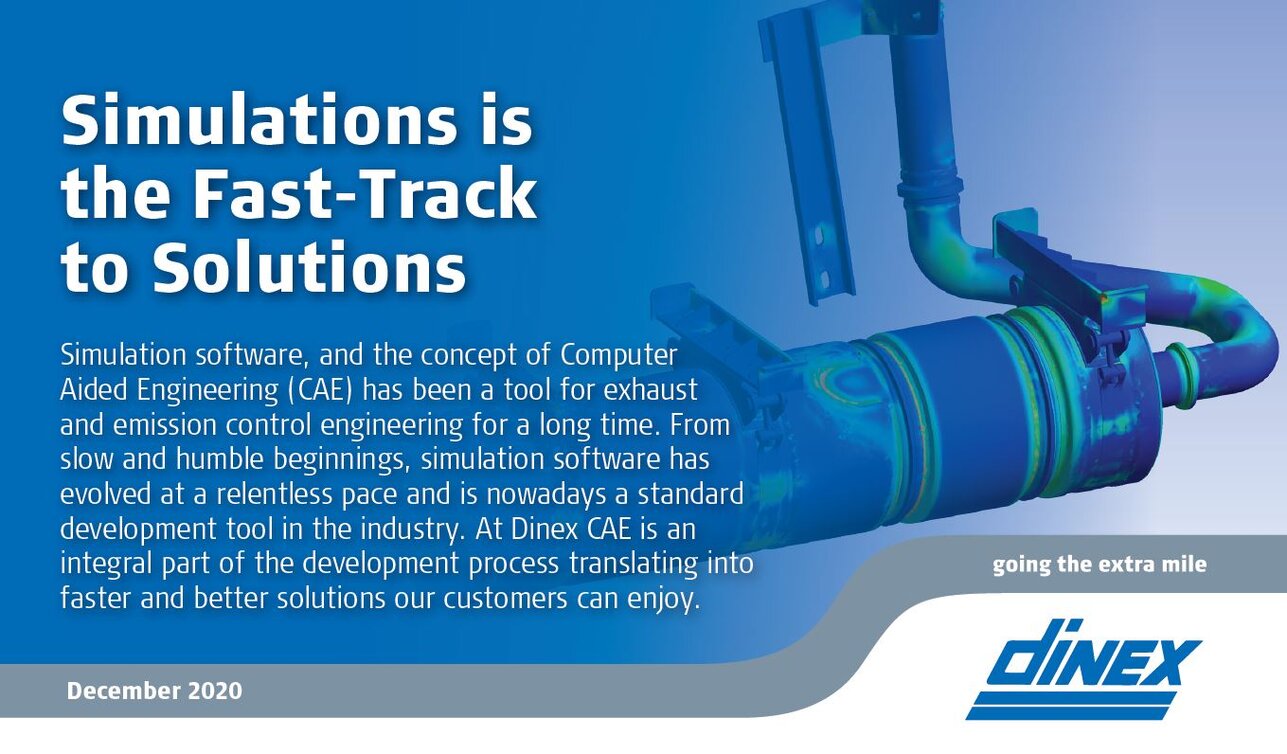
Simulation has been a valuable tool for the design of aftertreatment system canning components for quite some time at Dinex. A broad package that covers Computational Flow Dynamics (CFD) simulations to evaluate flow uniformity and pressure drop, to transmission loss, harmonics and other levels of mechanical design like Finite Element Analysis (FEA). At our headquarter offices in Denmark an entire team of skilled professionals has over 20 years of experience in applying the full simulation toolbox to create better solutions for our customers, in a faster, agile and efficient development process with less backflows.
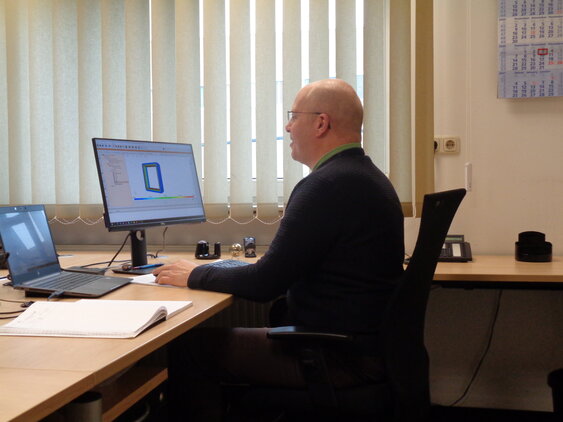
Emission Simulation
Emission simulation focuses on non mechanical aspects, more specifically it dwells into the kinetic and thermodynamics of the chemical reactions happening in the catalyst. At our R&D facility in Germany, we have a team of specialists leading the development of our own emission models.
Exhaust emission modelling digs deep within the physical and chemical effects that takes place on the catalysts.
Our simulation software has a comprehensive library of generic reactions for all existing catalyst technologies within Dinex, allowing for fine tuning into accurate reaction models that help the product development and application teams to deliver solutions to our customers problems, even before practical experiments take place.
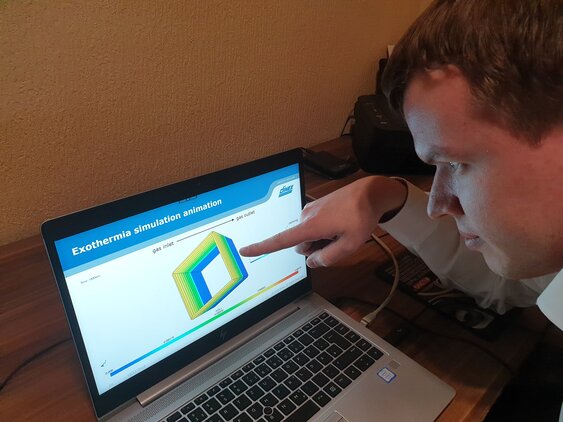
This tool allows for the evaluation of transient effects, typical of the conditions our catalysts are exposed to. This includes Oxygen storage, NOx storage, and Ammonia adsorption, as well as washcoat diffusion effects.
What is best, is that it opens the possibility of further development aimed at building very tailored models that are so representative of how our product works, that they can be used to predict performance at a very sophisticated level, saving countless hours and months of expensive testing.
But does it work?
Thanks to our long history of working extensively with both simulation tools and full size emission testing we have built an extensive database of knowledge and experience that forms the backbone of our models, allowing for the continuous closing of the gap between theoretical and practical results. As can be seen in Fig. 1 and Fig. 2 we have come a very long way already, and we will continue to improve so our customers can enjoy a fast and safe route to the right solutions.
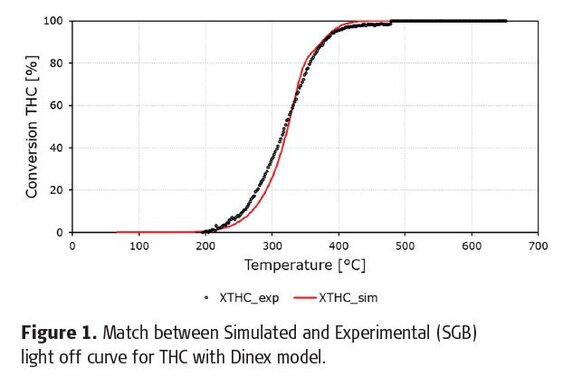
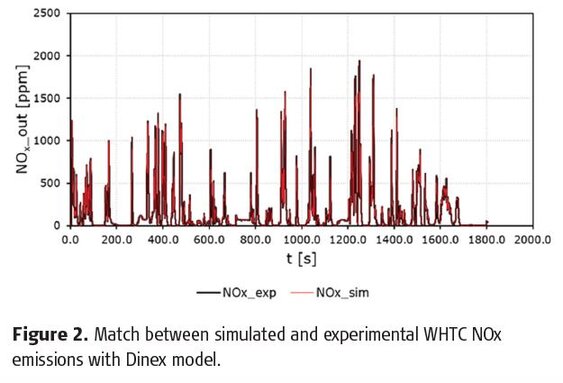
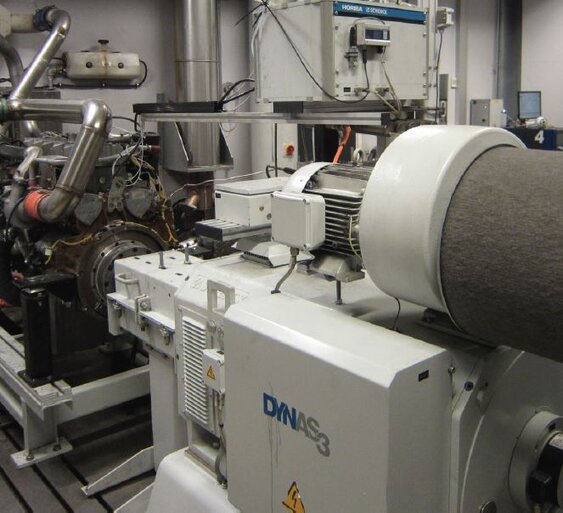
Want to learn more? Don’t hesitate to reach out to our CSO Mr. Lennart Rasmussen or our CTO Mr. Evangelos Georgiadis.
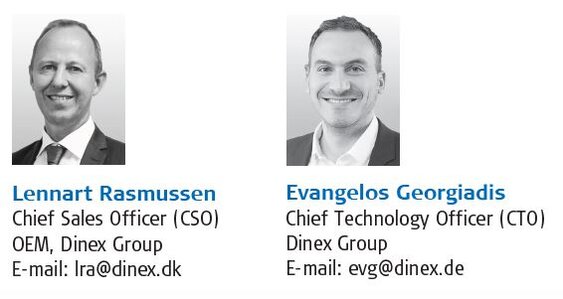
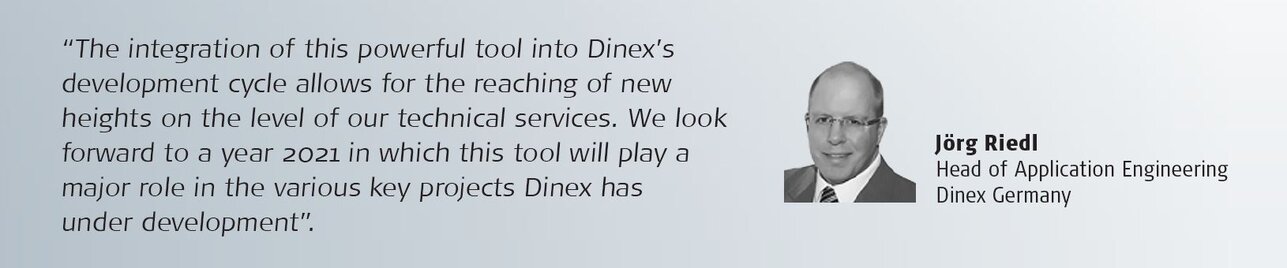